[ad_1]
At first look, trend and trade might not appear linked. But, Dutch artist and designer Iris Van Herpen has efficiently bridged the 2 worlds. By borrowing manufacturing methods from trade akin to 3D printing, laser slicing, and robotics, the artist goals to be a pioneer in making use of new applied sciences to high fashion. Her work is at present showcased on the Musée des Arts Décoratifs in Paris (till April twenty eighth). We visited the exhibition and located parts that resonate with the economic professionals in our readership.
At DirectIndustry, we’re extra accustomed to discussing technological improvements utilized to the economic world than to the style sector. Nevertheless, after attending the Iris Van Herpen exhibition on the Musée des Arts Décoratifs in Paris, it’s clear that we now have discovered a number of connections between the world of trade and the world of high fashion.
Artwork and Business
Along with her breathtaking clothes that includes distinctive designs, 39-year-old Dutch artist Iris Van Herpen bridges the worlds of artwork, science, structure, and trade. She has collaborated with a number of corporations and organizations that we frequently interview, akin to Stratasys, MIT, NASA, and Delft University. She even designed the Phantom Syntopia, a unique couture car model for the Rolls-Royce car model.
The designer creates her clothes not with conventional stitching methods and supplies, however with instruments extra generally present in factories (laser slicing machines, 3D printers, robots) than in designer studios.
We realized that if the artist makes use of industrial processes to create distinctive works, the industrialist can also be able to creating aesthetic, nearly creative items. Software program like Autodesk‘s, outfitted with AI, now affords extremely optimized automotive half designs for automotive producers, meant for 3D printing. Unusually, the ensuing elements at all times have very geometric, natural, and even creative shapes. Artwork and trade are finally not thus far aside.
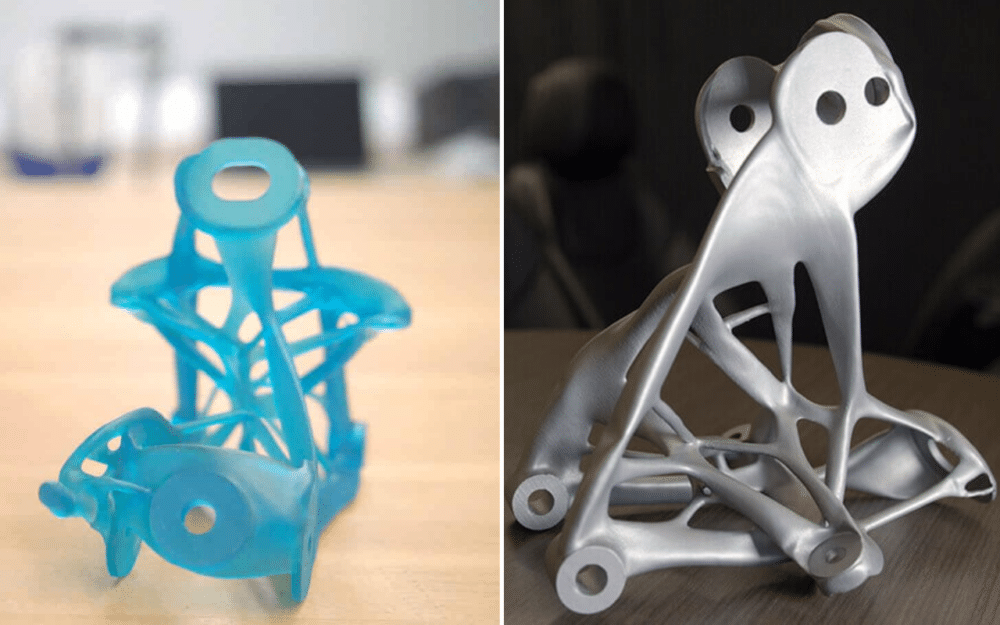
Due to this fact, we now have determined to give you this text on the technical and technological improvements mobilized by Iris Van Herpen to supply her magnificent clothes. Produced from supplies starting from blown glass to Plexiglas, laser-cut steel, and biodegradable supplies printed in 3D, these clothes are extra than simply high fashion. They stand on the intersection of science, design, structure, artwork, and trend.
Talking of structure, in 2019, the artist notably participated within the design of the wall facade of a constructing in Leiden (the Netherlands), the Naturalis Biodiversity Center. The constructing consists of 262 panels molded from concrete and marble powder.
Craftolution
Iris Van Herpen goals to be a pioneer in the usage of new applied sciences utilized to the world of high fashion. Till now, no artist has so seamlessly blended science, know-how, and trend.
By means of quite a few collaborations with researchers, architects, and engineers, Iris Van Herpen has succeeded in creating distinctive trend items impressed by nature, the human physique, marine biology, and even the Gothic structure of her nation. However she additionally attracts inspiration from trade. The particle accelerator at CERN and colourful photos taken by the James Webb telescope are only a few sources of inspiration for composing her works.
Conscious that the style trade and the textile trade on the whole are extraordinarily polluting, she additionally seeks to make use of biodegradable textiles, akin to banana peels and cocoa.
For her, know-how is a inventive instrument. She speaks of “craftolution”, a mixture of artisans and innovation. As a result of it’s due to the probabilities provided by new applied sciences that she has been in a position to translate into artworks issues as delicate and complicated to breed because the actions of the human physique or the motion of water.
We’ve chosen several types of industrial processes that she makes use of for her creations.
Thermoforming
Within the Splash Costume, the splash is a hand-formed plexiglass plate by the designer to offer it the looks of transferring liquid. Utilizing scissors, and pliers, she cuts, distorts, stretches, and shapes an inherently elusive and unattainable ingredient, pushing the boundaries of creativity in trend even additional.
Blown Glass
The Dimensionism gown is made from borosilicate glass, a glass extremely proof against warmth. It has been thermoformed and labored with a flame. For this, the designer may depend on the experience of a grasp glassblower, Bernard Weinmayer.
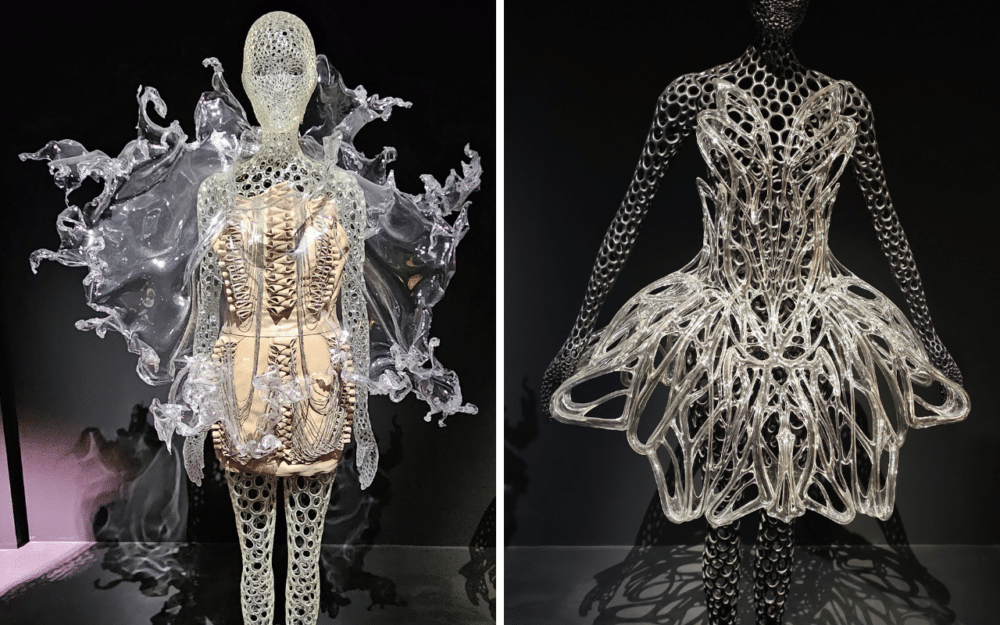
Laser Reducing and Water Jet Reducing
Lots of Iris Van Herpen’s creations make use of laser slicing or water jet slicing.
For instance, the Aeriform creation accommodates a set of geodesic spheres made from galvanized metal that was lower with a water jet. This assortment was impressed partly by CERN and the query of the power that outcomes from particle acceleration.
With the Magnetosphere gown, the artist makes use of plastic particles. Lower with a laser, this plastic discovered on seashores then varieties layers of lace.
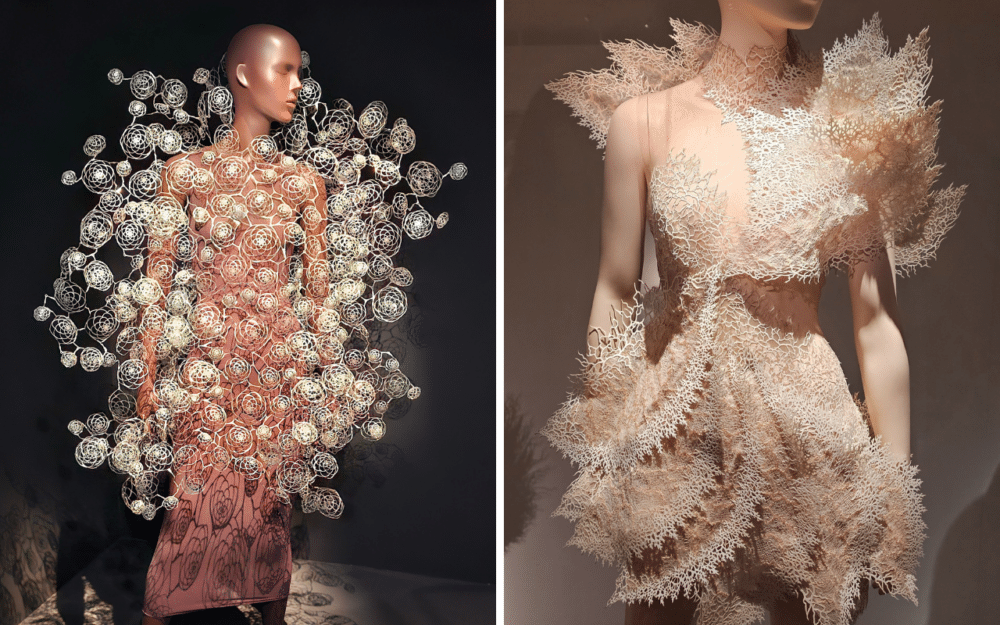
Robotics
In 2015, the artist enlisted three robots to print and weave a gown stay throughout a trend week occasion, worn by the Recreation of Thrones actress Gwendoline Christie.
The artist detailed the methods utilized in a press launch:
“The stay course of blends totally different methods – laser slicing, hand weaving, and 3D printing into one gown, which spreads from the middle, quaquaversal in its geometries.”
For the event, three ABB IRB 2600 robotic arms had been used. She collaborated with the College of Innsbruck and their REXILAB robotic experimentation lab to allow this demonstration.
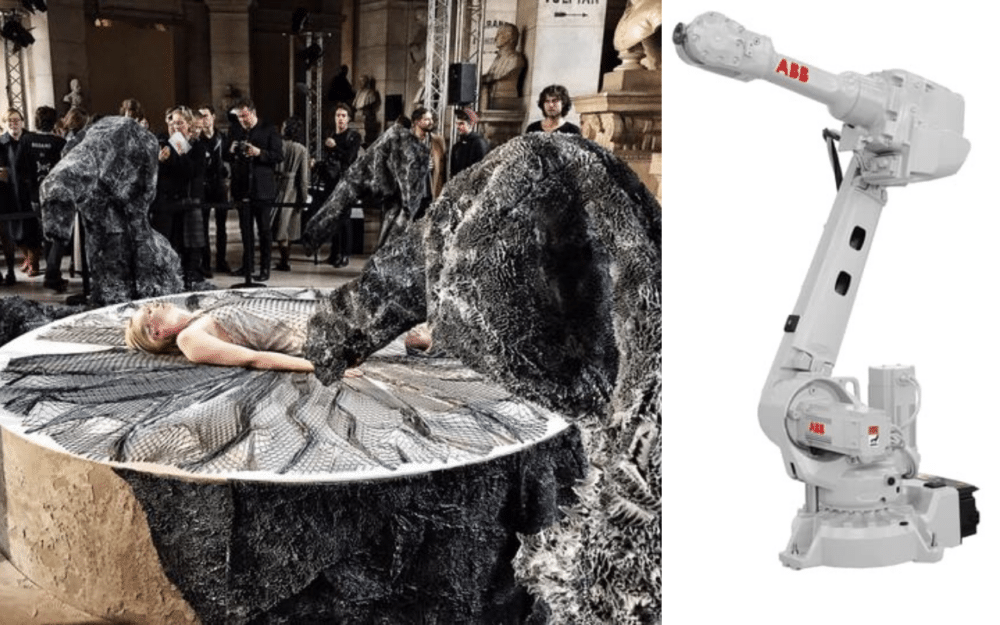
3D Printing
Iris Van Herpen started experimenting with additive manufacturing within the 2010s. On the time, she needed to create a water gown however didn’t know the way to obtain the liquid impact with accessible textiles.
“I couldn’t make the water gown in any method with a needle and a thread. About the identical time, I noticed architects making their maquettes with 3D printers. I turned fascinated by this pioneering course of and thought this may very well be my resolution,” she recounted in an interview with Hans Ulrich Obrist.
At the moment, Iris Van Herpen is the designer who makes use of 3D printing probably the most in her work.
Listed below are some examples of 3D-printed creations and the totally different printing applied sciences concerned.
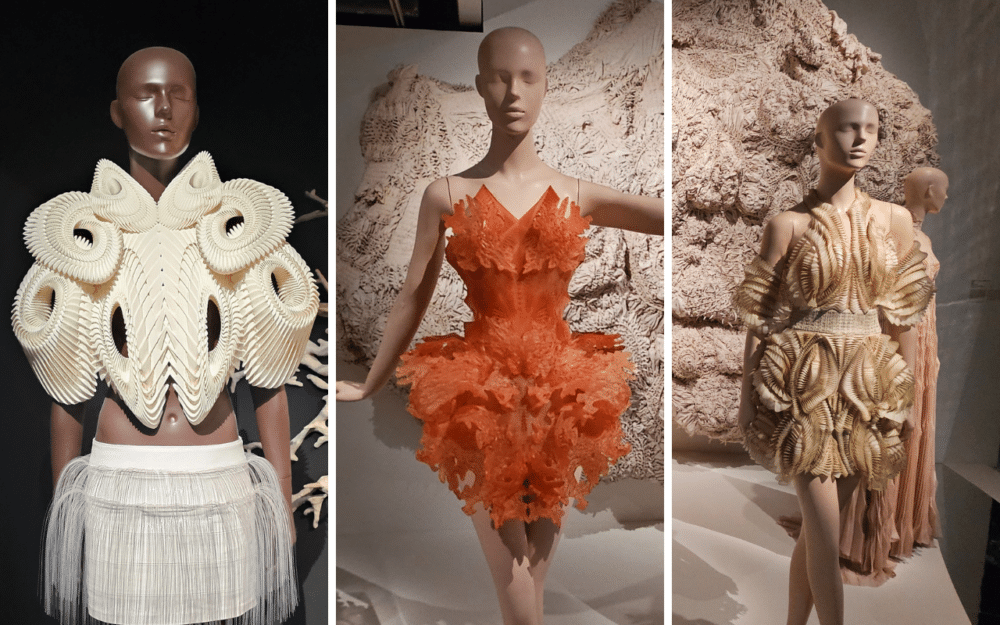
Crystallization: SLS Expertise
In 2010, she collaborated with architect Daniel Widrig and digital producers MGX by Materialise. The concept was to discover digital design methods and digital fabrication utilized to the world of high fashion. The primary 3D-printed accent, the ‘Crystallization‘ prime, was unveiled at Amsterdam Style Week in 2010. Impressed by shell constructions and fossils, it’s 3D-printed from white polyamide utilizing SLS (Selective Laser Sintering) know-how at 0.1 mm thickness. It took 6 full days to print the garment.
In 2013, she introduced two 3D-printed ensembles at Paris Style Week in acrylic and polyurethane impressed by coral. The skirt and cape had been produced utilizing Stratasys’ distinctive Objet Connex multi-material 3D printing know-how. This allowed a wide range of materials properties to be printed in a single construct. Each exhausting and gentle supplies had been included inside the design.
To attain this feat, she collaborated with Neri Oxman. On the time, he managed the now not energetic Mediated Matter Group at MIT in Boston.
Hybrid Holism: Mammoth Stereolithography
In 2012, she collaborated with the corporate Materialise to make use of a brand new approach, Mammoth Stereolithography (MSL). This 3D printing know-how makes use of UV rays to harden polymer supplies. Because of this know-how, it was doable to acquire honeycomb patterns.
Foliage: PolyJet
In 2018, Iris Van Herpen collaborated with the Delft College of Expertise to make use of a course of able to concurrently printing totally different supplies, a property of the corporate Stratasys, known as PolyJet know-how. This method allowed for the creation of a gown through which petal-shaped patterns of 0.8 mm had been instantly 3D printed onto tulle. 260 hours had been required to print the gown.
Digital Modeling
In 2020, the artist additionally turned to modeling instruments to just about create her clothes. This observe is often present in structure or trade.
For the Morphogenesis gown, for instance, she relied on the Rhinoceros instrument.
Printing with Eco-Pleasant Supplies
The textile trade, to which high fashion belongs, is likely one of the most polluting on the earth. We’ve beforehand reported on the havoc wreaked by this trade by way of water useful resource wastage and dye air pollution. Moreover, clothes, composed of supplies that aren’t absolutely recyclable, typically find yourself in overcrowded landfills in third-world nations.
Conscious of the environmental influence of her discipline, Iris Van Herpen seeks different supplies. She already incorporates plastic waste, notably by means of collaboration with Parley For the Ocean. However she additionally explores different potentialities, together with extra natural, biodegradable textiles for her creations. Right here once more, know-how involves the rescue to make this doable.
For her 2022 challenge, Singularity, the artist teamed up with Eric Klarenbeek and Maartje Dros. Collectively, they developed a biotechnological technique for 3D printing natural substances akin to algae and mycelium. This collaboration resulted in a number of clothes created from leftover cacao bean shells reworked into biopolymers and printed as filaments.
For her Metamorphism creation, she designed clothes composed of sustainable off-white banana leaf materials.
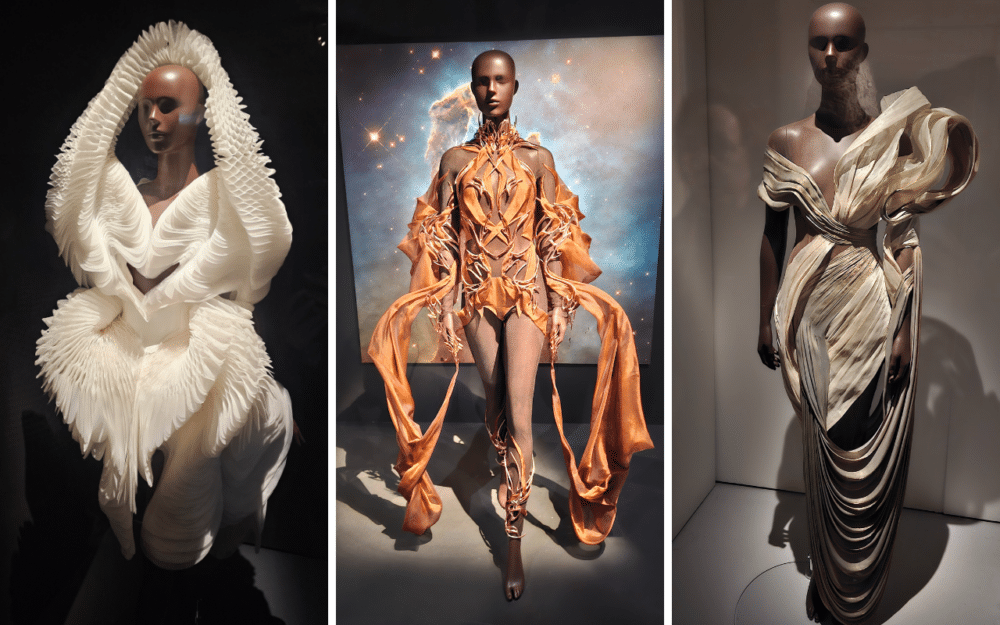
And Tomorrow, 4D Printing?
Iris Van Herpen is now exploring 4D printing. A couple of years in the past, we printed an article concerning the established Self-Assembly Lab of MIT and two of the most important names in printing—Stratasys and Autodesk.
On their web site, the Self-Meeting Lab detailed the 4D printing idea.
“With a single multi-material print, a product or mechanism can remodel from any 1D strand into 3D form, 2D floor into 3D form, or morph from one 3D form into one other. Utilizing solely water, warmth, gentle, or different easy power enter, this method affords adaptability and dynamic response for constructions and methods of all sizes.”
For Iris Van Herpen, the concept is to create clothes whose supplies are able to evolving over time, responding to motion, very like vegetation, for instance. She collaborates notably with Philip Beesley, the designer of the dwelling structure system or hylozoism.
Whereas 4D printing applied sciences are nonetheless below growth, each the artist and industrialists carefully monitor improvements on this sector.
[ad_2]
Source link